2.液力电控自动变速器液压循环原理
自动变速器要比手动变速器寿命短,因为所有的自动变速器都存在
液压系统的“死亡循环”,而且这个循环是从新车开动那一时刻就开始了,一直到变速器的寿命结束。如何来延缓自动变速器“死亡循环”的时间呢?在正常使用情况下我们一般的做法是及时更换
ATF,一是因长时间高温下变质的
ATF会带来
液压系统压力的异常,导致元件异常磨损;二是更换滤清器,带走一部分机械部件磨损下来的比较粗的颗粒,净化
ATF状态。为了更进一步说明自动变速器液压循环系统的重要性,我们对冷热循环系统加以细致说明,并且把此循环系统称之为 “自动变速器生命周期循环图”(图7),从而分析一个正常自动变速器如何从“冷循环”到“热循环”至“恶性循环”再到 “死亡循环”的过程。
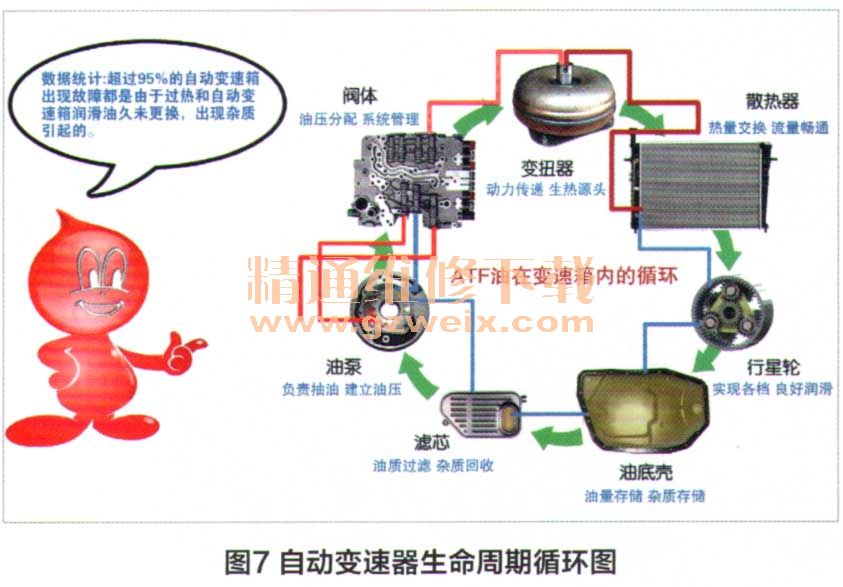
大多数自动变速器都会有一个下置式油底壳,它主要用来存储适量的
ATF以及收集一些变速器内的杂质。发动机运转后带动自动变速器油泵一起旋转,油泵会把油底壳内的
ATF通过滤清器的过滤,抽上来并压出去,这一过程中滤清器不仅起到油质过滤的作用,还要实现杂质回收,因此我们把油底壳内的
ATF和滤清器称之为“以油泵为核心的上游控制”。油泵负责抽油并建立油泵油压的工作,油泵压出去的液压油流向变速器的“心脏”—阀体(油路板)的主油压调节阀处,以便形成变速器的系统油压。阀体相当于自动变速器
液压系统的油压分配及系统管理中心,它把调节好的变扭器工作油压输送至液力变扭器内。变扭器的任务是完成发动机的动力传递过程,但它又是一个热源体,做功后的热油必须去冷却系统进行热交换,因此无论是集成式冷却器还是独立式冷却器,它的功能就是确保流量和热交换,经过热交换后的
ATF又回到变速器需要润滑的机械部件上(特别是行星齿轮机构),由于其属于常啮合齿轮组,时刻需要良好的润滑,否则变速器将无法实现各挡工作。齿轮润滑后的油液自然又回到油底壳内,这样便完成一次整体循环过程。
变速器长时间不保养会对哪些系统或者哪些部件带来损伤?自动变速器长时间高温后
ATF的整体性能就会随之下降,性能变差的
ATF在液压循环中首先影响的是机械元件。当润滑条件变差时机械元件自然会形成磨损,磨损下来的颗粒一部分被滤清器和冷却器所收集,一部分细微的颗粒会随着油液的循环进入到变速器的核心部位,即变速器的阀体内。滤清器收集的颗粒越多,其过滤能力就会越来越低,从而影响油泵的抽油能力和油泵本身的润滑质量。油泵抽油能力下降,导致
液压系统的压力调节功能失调,这样变扭器本身的能耗损失也越来越大,变速器温度持续升高。当冷却器内的颗粒越来越多时变速器的热交换能力以及润滑流量会受到影响,这样变速器温度会越来越高,同时行星齿轮机构因得不到良好的润滑而加剧磨损,磨损下来的更多颗粒进入滤清器,造成严重堵塞情况,此时油泵难以正常工作,变速器因无油压而停止动力传递过程,变速器最终进入“死亡循环”。另外,在滤清器未完全堵塞之前,如果有细微的颗粒进入液压控制单元(阀体)后会导致阀门的卡滞或磨损,包括电磁阀的卡滞或磨损,因此导致变速器提前损坏。接下来我们分别就
AT、
CVT和
DCT三款变速器的热源及润滑条件加以分类说明。
AT变速器无论是行星齿轮式还是本田平行轴斜齿轮式,它们均存在一个液力传递过程,即都带有液力变扭器的变速器。因此
AT变速器在工作过程当中变扭器是最主要的热源体,特别是在液力传递中产生大量的热能。从变扭器结构与工作原理方面(图8)我们了解到:变扭器的泵轮由发动机带转,油泵轮上面的叶片带动
ATF产生动态液体离心力(机械能到液压能的转换),由泵轮叶片的外部边缘将带有离心压力的
ATF甩向与泵轮对置的涡轮上,涡轮在
ATF离心力的作用下开始旋转(液压能到机械能的转换),当变速器挂入动力挡后由于涡轮与变速器输入轴刚性连接,因此动力流生成车辆可以行驶。在此过程中由于泵轮与涡轮之间存在一定的转速差,这部分转速差是液体带来的能耗损失,而且转速差越大能耗损失也会越大,因此产生的热能就会越多,所以变扭器是
AT最主要的热源,这也是变扭器的输出端与冷却系统建立连接的原因。
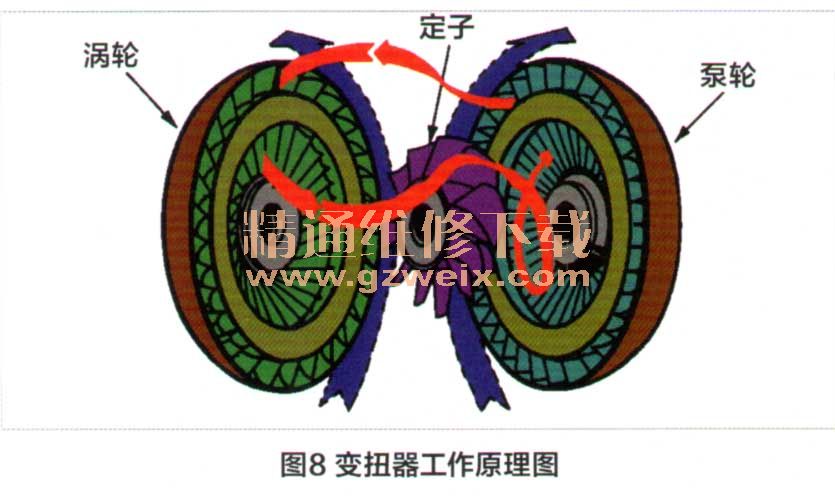
除了变扭器生热之外,在
At变速器当中还有终端元件(离合器和制动器)工作过程中摩擦带来的热(图9),试验证明摩擦片摩擦时瞬间带来的热高达200~300℃,因此如果离合器或制动器工作中存在打滑或滑膜时间过长会导致变速器进入高温状态。
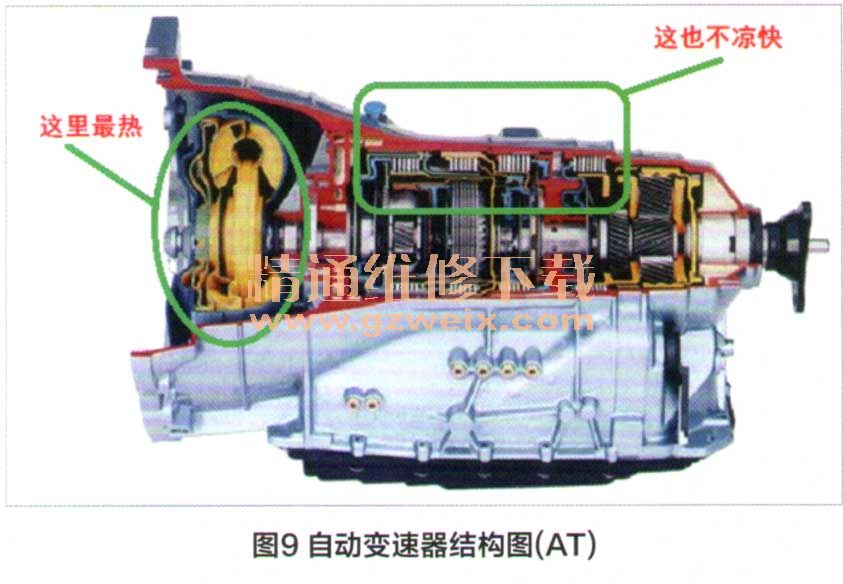
关于
AT变速器的润滑条件或润滑要求,前面我们讲述了行星齿轮机构的润滑,其实所有需要润滑的部件都叫润滑部件,比如轴与轴套之间、阀门与阀孔之间、摩擦片与钢片之间、轴承与垫片之间等,因此涉及到旋转、移动或摩擦的元件都需要良好的润滑过程。
上一页 [1] [2] [3] 下一页