不同的铸造工艺对产品结构有不同的要求,结构设计不仅需满足功能性要求,还需保证铸造工艺及铸造性能的要求。合理的结构,不仅能提高产品设计强度,还可简化铸造工艺,提高生产效率、改善铸件质量、降低产品成本。后盖壳体是重型汽车变速器中的重要部件之一,起到传递扭矩的作用,壳体轴承支承孔处受力复杂,如果失效则造成整车无法运行等问题,严重影响汽车行驶的安全性能。因此,在铝合金轻量化进程中,对后盖产品结构的合理性提出了更高要求。
本文以某重型汽车变速器后盖壳体为例,重点介绍了重力铸造一消失模工艺与压铸工艺对产品结构的要求,根据各自的工艺特点,对产品结构进行调整,不仅满足了性能要求,同时满足了铸造工艺的要求。
一、壳体壁厚
原消失模工艺作为重力铸造的一种,产品形状不受传统铸造工艺的限制,但对其最小壁厚有一定要求,若产品太薄,
EPS成型过程易受到阻碍;浇注过程易过早凝固,造成产品内部或外部缺陷;产品在转运、成型过程中易变形,造成产品报废。
后盖壳体结构如图1a所示。该壳体尺寸367x292x 155mm,采用消失模工艺,材料为ZL101A铝合金,经现场验证,平均壁厚设计为8mm较为合理,产品质量6.3kg。
对于压铸工艺,由于该工艺为高速高压充型,金属液的充填能力及压实效果大大提高,可以充填细节部位,可生产薄壁零件;又因压铸件表面受激冷作用强,表面致密,内部组织粗大,弥散多孔特点,若壁厚太厚,将会产生“压不实”现象,内部出现缩孔,影响产品质量。因此,合理的壁厚,对其压铸工艺尤为重要。
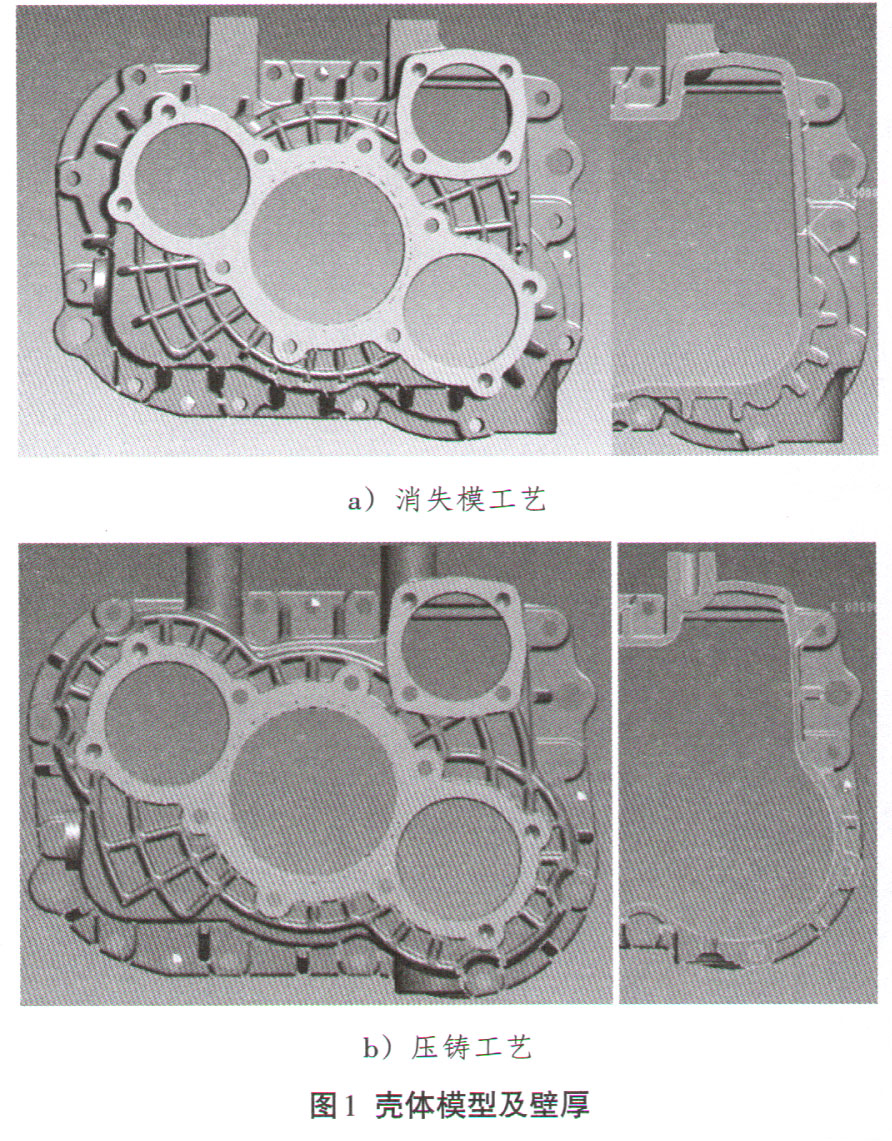
后盖壳体改用压铸工艺后,如图1b所示,材料选择ADC 12,平均壁厚设计为6mm,质量5kg,比消失模工艺质量减少20%。对于局部厚大部位及内部质量要求高的部位进行优化,例如图2所示,降低后盖与变速器壳体连接面厚度,壁厚从原来的15mm变为10mm;如图3所示,将其结合面局部进行“瘦身”设计,尽量保证产品壁厚的一致性。
二、分模方式
消失模工艺为结构设计提供了充分的自由度,可通过泡沫模片组合成各种高难度的复杂产品,对其分模方式要求低。后盖壳体采用消失模工艺时,结构相对简单,如图4所示,对于周边各孔,可不铸出,后续采用机加工方式实现,外部采用整块模芯,简化了模具结构;图4中的倒扣结构,采用模具活块或泡沫拼接即可实现,成本低。
采用压铸工艺后,产品分型面选在结合面位置,周边侧孔需铸出,采用侧滑块抽芯机构实现,模具复杂;对于内部倒扣结构,若采用内抽芯,自动化程度低,故障率及模具造价高。因此如图4所示,直接取消倒扣结构,扩大内部空间,采用整块模芯,极大的简化了模具。
三、拔模斜度
后盖壳体采用消失模工艺时,因白模成型过程中,
EPS泡沫弹性大,设计者可设计较小的拔模斜度或局部不设计拔模即可实现脱模;采用压铸工艺时,因模具及合金均为刚性材料,需充分考虑拔模斜度,此壳体内部及外部深腔部位拔模斜度最小需设计1.5°-2°左右,确保产品在生产过程中能够顺利脱模,不会造成拉伤及变形;增加拔模斜度后,设计需充分考虑装配空间,以免出现干涉情况,如图5所示,对于螺栓连接部位,消失模工艺因其拔模斜度小可不用设计避让,压铸工艺需考虑避让。
关键词: