g)对于踏板摩托车,由于发动机多采用卧式发动机,拆装时多有不便,且部分铝合金制造的
气缸盖半圆槽圆弧加工过浅,凸轮轴及摇臂座装上
气缸盖相关位置紧固螺母(螺栓)后,不但会造成摇臂座半圆槽变形,同时也会在
气缸盖半圆槽圆弧底面留下明显的压痕,影响凸轮轴组件中滚动轴承的正常运转。为此,只有用合适的细圆锉刀或小半圆铲刀,在
气缸盖半圆槽孔处轻轻刮铲所有亮点。实在没有这些工具时,也可用砂纸在发亮部位轻轻擦去亮点。如实在无法消除这些亮点或即使消除了亮点,异常声音仍然存在,可利用超市购买的易拉罐外包装,根据摇臂座与
气缸盖的安装尺寸,剪下其铁皮(有的材料可能是铝皮,厚度约0.05~0.08 mm,注意将铁皮或铝皮的毛边锉修干净,避免此处有毛刺),垫放在摇臂座(定位销)平面与
气缸盖半圆槽平面之间,确认没有挡住润滑油道,最后按照规定的扭矩紧固摇臂座螺母即可。不过,在按照这个方法装配凸轮轴及摇臂座组件后,必须起动发动机,在怠速状态下仔细鉴别其运转声音如图53所示,是否有所好转。否则,应视情予以检修或更换相关零件。

当然,有部分凸轮轴轴承发出的异常声音与轴承的滚道受伤紧密相连的,部分轴承(分解前的凸轮轴及轴承如图54所示)须在分解后才能发现其滚道上的受伤痕迹(如图55, 56所示)。这就需要大家在平时的维修过程中逐渐积累经验,不断提高判断故障异声的鉴别能力。
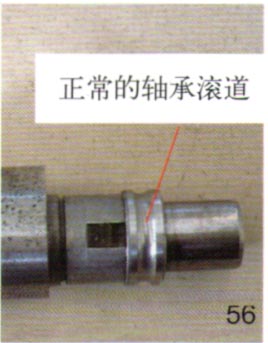
h)部分凸轮轴两端支撑采用的是衬套(譬如:CB125T双缸摩托车),行驶数万km的摩托车,其凸轮衬套孔同样也会在多次拆装过程中,产生不同程度的变形。由于衬套与凸轮轴颈之间须留0.083~0.116 mm的油隙,其松紧程度很难把握。为此,建议在更换凸轮轴后,有条件时,分别用数显游标卡尺测量凸轮轴两端轴颈和衬套内孔尺寸。没有测量器具时,可将其衬套空套于凸轮轴两端轴颈,用手指扳动衬套,感觉其在凸轮轴两端轴颈的实际间隙。然后,将凸轮轴套装上正时链轮,连同衬套放到
气缸盖半圆槽中(注意暂时不装正时链条,便于转动凸轮轴),再将拆去气门摇臂的摇臂座(便于转动凸轮轴时不受干扰)装上,按照各型摩托车发动机使用说明书规定的扭矩紧固
气缸盖螺母。紧固好所有
气缸盖螺母后,先用手指捏住、拨动正时链轮,感觉凸轮轴在其衬套内是否有间隙,确认有间隙,再快速转动正时链轮及凸轮轴,此时注意观察凸轮轴在衬套内的运转是否灵活,以及运转声音有无异常。如果凸轮轴在快速转动过程中有时快有时慢,或在运转过程中发出“咯咯”的声音,说明衬套在摇臂座压紧后存在变形现象。应视情予以检查或更换相关零件,直到此项试验正常为止。
i)上述介绍的实际装配鉴别法,同样也适用于踏扳摩托车凸轮轴及轴承的检查。不过,应先对在轴承进行静态检查,即将轴承按照捏住轴承的内圈,用力扳动轴承外圈,不应有明显的间隙(一般滚动轴承的原始游隙只有5~20 p m),然后再快速转动轴承外圈,仔细倾听轴承的运转声音,应是很轻微的、不细心静听几乎听不到的声音,同时手上几乎感觉不到轴承运转时产生的震动。在这个基础上,将凸轮轴及轴承组件和摇臂座组件(暂不装摇臂)装到
气缸盖半圆槽中,按照规定的扭矩紧固
气缸盖螺母,再按照上述方法进行比较鉴别。或许有部分维修人员不愿意接受表面看上好象烦琐一点实际装配鉴别方法,但这个能够辨别出故障点的方法,确实是费的时间,但总比无目的、无休止的更换配件要好得多,有兴趣的朋友不仿一试。
j)本田CG125摩托车发动机因其结构的特殊性,凸轮轴装在左曲轴箱专用孔中,配装了与曲轴正时齿轮啮合的凸轮轴齿轮,该组啮合齿轮在设计时无淬火和热处理要求,属于软齿面状态,这无疑对此处的润滑提出了更高的要求,故在左曲轴箱上特别设计了一个小油池(如图2所示),使曲轴正时齿轮、凸轮轴及齿轮均浸抱在机油内,以满足运动摩擦副的润滑要求。由于很多用户不清楚小油池的作用,在更换曲轴箱润滑油时,不知道如何放尽小油池内的脏润滑油,使凸轮轴及齿轮磨损加剧,严重时,凸轮轴的顶高(升程)被磨去不少(如图57~59所示),从而引起摩托车加速性能下降,且发出异常声响。若不及时更换左曲轴箱小油池内的润滑油,凸轮轴换上使用不久,其凸轮轴及齿轮部分因小油池的润滑油严重变质而磨损加剧。按照正规的换油方法,需拆去CG 125发动机左盖、飞轮组件、启动大链轮和压销体组件等零件,一般要到维修站使用专门的拆卸工具才能进行更换。对于绝大多数用户来说自行更换确实比较困难,保养工作也难以保证质量,一旦操作失误,还会带来故障隐患和严重后果。为此,建议采用如下简便方法进行换油。
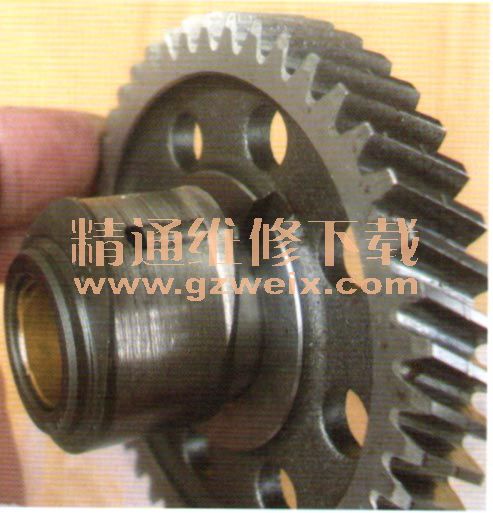
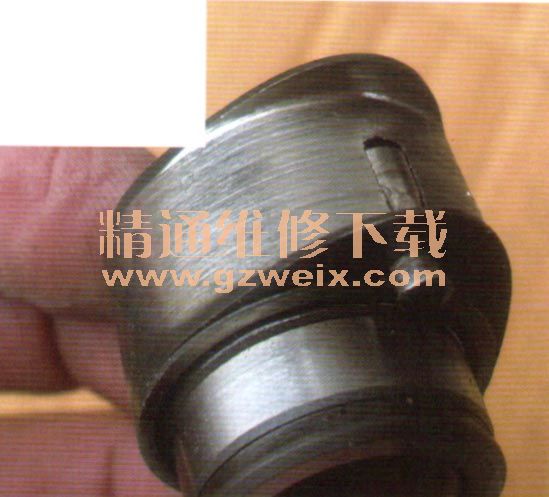
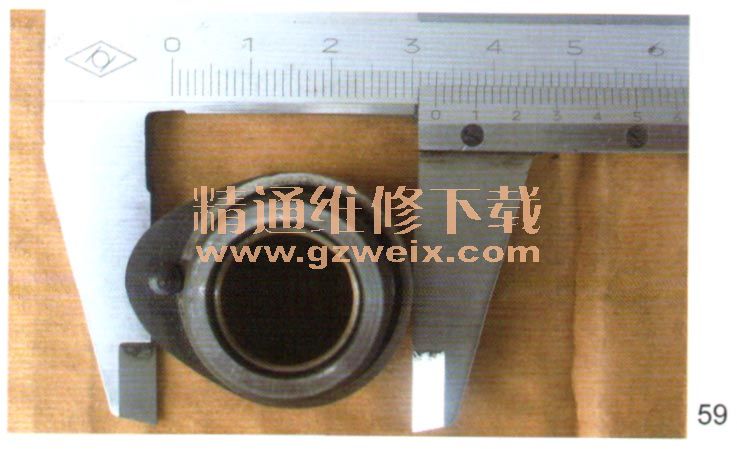
上一页 [1] [2] [3] [4] [5] 下一页